Composite Materials
Composites
are materials that are mixtures of two or more components which are
essentially insoluble in each other. The components are taken from the
fundamental structural material types: metals, ceramics, glasses,
polymers. The result is a material that has superior properties to
any of the constituents alone: "The best of both worlds."
Many composites have
just two components: A matrix phase with some kind of dispersed phase. The
classic example of a composite material is fiberglass which consists of
micron-scale reinforcing glass fibers in a polymeric matrix material.
Fiberglass has
the high strength of its glass fibers combined with the high ductility
of its polymeric matrix. This is because the two materials were
combined in the right way. Imagine if they were combined in such a way
as to obtain a composite material that was both weak and brittle! The
geometry of how composites are combined is just as important as their
constituent materials and the relative amounts.
The Matrix Phase
Although there are exceptions, in general the
purpose of the matrix phase is to transfer the load to the
fibers, prevent propagation of brittle cracks, separate the fibers
and protect them from surface damage. Usually Ef >>Em and the matrix is reasonably ductile.
There are 3 catagories of composites based on the matrix material:
- PMC - Polymeric Matrix Composites
These are relatively cheap and easy to fabricate. Their service temperatures are <200oC.
Examples include: - polyesters (cheap)
- vinyl esters (cheap)
- expoxies (more expensive but better properties and more resistant to moisture)
- polyimid resins (for relatively high temps)
- thermoplastic resins (for high temps)
- MMC - Metal Matrix Composites
These were developed to get high strength-to-weight ratios, better
performance at high temperatures and better conductivities. Although they are more expensive than PMCs, they have the advantages of being non-flammable, greater
resistance to degradation by organic fluids, good ductility and good load bearing capabilities.
- CMC - Ceramic Matrix Composites)
These were developed
to get improved strength and toughness for high temperature applications. CMCs differ significantly from the others
in that the purpose of the reinforcing fibers is to increase ductility,
not strength. The
mechanism by which these materials are toughened is that the
reinforcing fibers interfere with crack propagation in the brittle ceramic matrix. This can
happen by crack deflection, crack bridging, or fiber pullout.
The Dispersed Phase
The
dispersed phase has a geometry that is either:
- aggregate particulates
These are more or less equi-axed
particles dispersed throughout the matrix phase.
- fibers
These are long, axial particles dispersed throughout the matrix phase in aligned or random arrangements.
Although
we won't consider these here, some
composites have other more complicated arrangements of
fibers that take advantage of sophisticated
geometries to gain desirable properties. Examples of these more
complicated composites are woven fabric layers
interspersed with a matrix phase or honeycomb stuctures.
Composite Properties
The properties of the resulting composite material will be dependant on:- the properties of the constituents
- the relative amount of each constituent
- the geometry (i.e. shape, size, orientation and distribution of dispersed phase)
Superior Properties of Composites Compared to Non-composites
Consider
these two plots.
The first shows that the specific strength of epoxy is
substantially increased by adding a dispersed phase.
The second shows a substantial increase in fracture toughness of ceramics by the addition of a reinforcing phase.
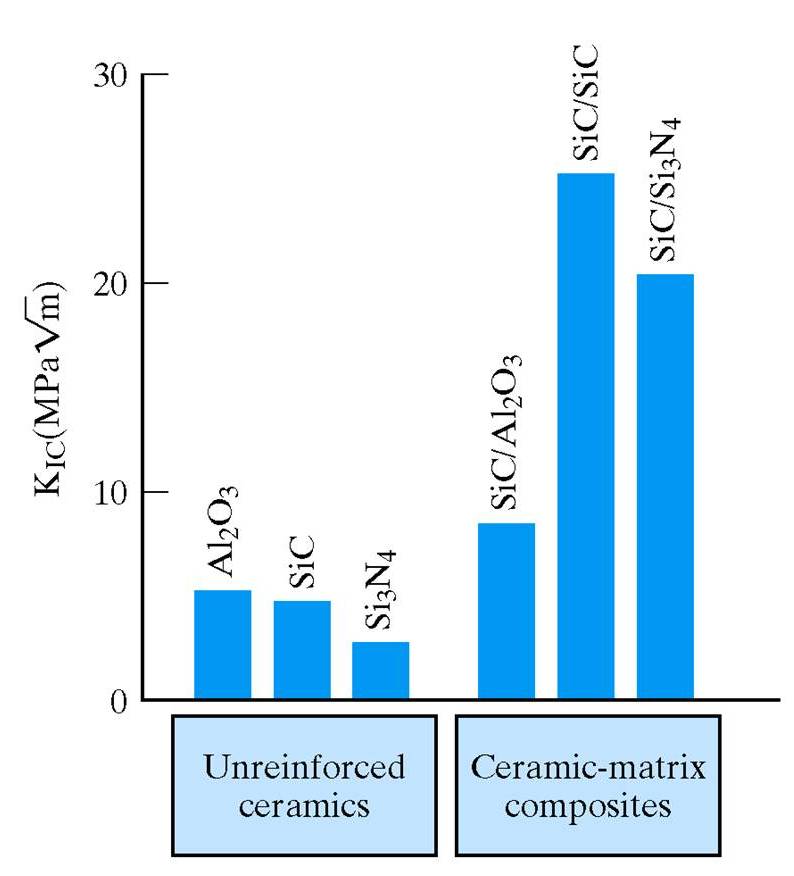